An Unbiased View of Die Castings
Wiki Article
The Buzz on Die Casting
Table of ContentsThe smart Trick of Oem That Nobody is Talking AboutSee This Report on Plastic Manufacturing4 Simple Techniques For Mfg6 Easy Facts About Mfg DescribedFacts About Manufacturing UncoveredTop Guidelines Of Plastic Manufacturing
The text on this page is a sample from our full White Paper 'Injection Moulding for Purchasers' - * Sample text * - for full guide click the download button above! Introduction This overview is planned for individuals that are looking to resource plastic mouldings. It offers a much required insight right into all that is involved with developing plastic components, from the mould device required to the moulding procedure itself.If you desire to discover further, the overview covers kinds of mould devices, in addition to special finishing processes such as colours & plating. Words that are underlined can be located in the reference in the appendix ... Component I: Moulding: The Basics The Advantages of Injection Moulding Plastic shot moulding is an extremely exact process that offers a number of advantages over various other plastic handling techniques.
Precision is perfect for very intricate parts. Contrasted to various other methods, moulding permits you to include more functions at extremely tiny tolerances. Have a look at the image to the. You can hold this moulding in the hand of your hand as well as it has bosses, ribs, steel inserts, side cores and also holes, made with a moving shut down function in the mould device.
The Greatest Guide To Mfg


How Oem can Save You Time, Stress, and Money.
from material feed & melting; material injection; cooling time and ejection to the re-closing of the mould tool ready device all set next cycleFollowing Draft angles - The wall surfaces of a moulded component ought to be a little tapered in the instructions in which the component is expelled from the mould tool, to enable the part to be expelled conveniently.Ejector stroke - The pressing out of ejector pins to eject the moulded part from the mould tool. Ejector stroke rate, length as well as timing needs to be thoroughly controlled to avoid damage to the ejectors and mould tool, but at the same time make the moulding cycle as brief as feasible.
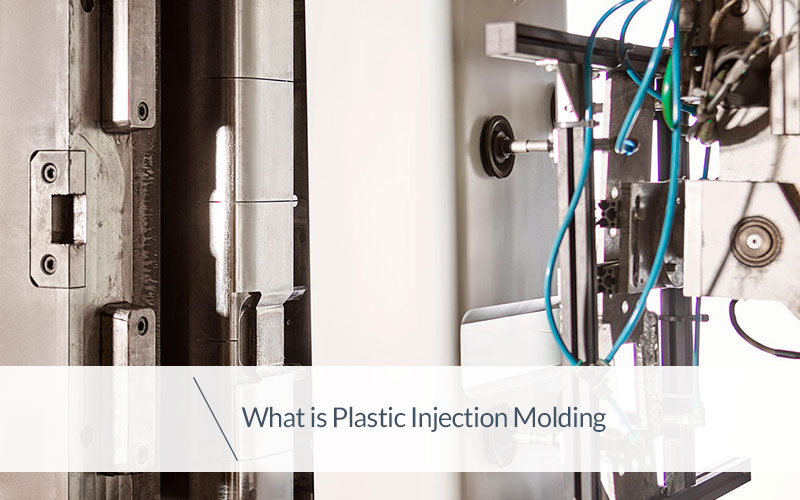
The Of Lean Production
Ribs - When a plastic part has thin walls, ribs are included in the style to make the thin walls more powerful Side cores - smart manufacturing Side activity which produces an attribute on a moulded part, at an opposing angle to the typical opening instructions of the mould device. mfg. The side core requires to be able to retract as the plastic component can not be expelled or else.
Walls - The sides of a moulded part The text on this page is an example from our complete White Paper 'Injection Moulding for Buyers'.
Manufacturing procedure for generating components by infusing molten material into a mould, or mold Simplified representation of the procedure Injection moulding (united state punctuation: shot molding) is a manufacturing process for creating parts by injecting liquified product into a mould, or mold. Injection moulding can be done with a host of products mainly consisting of metals (for which the procedure is called die-casting), glasses, elastomers, confections, and oem brand most frequently polycarbonate and thermosetting polymers. Injection moulding is commonly used for producing a variety of components, from the tiniest elements to whole body panels of vehicles. Injection moulding uses a special-purpose device that has three components: the injection device, the mould as well as the clamp.
Facts About Additive Manufacturing Uncovered
Refine characteristics [modify] Shot moulding makes use of a ram or screw-type bettor to require molten plastic or rubber material into a mould dental caries; this strengthens right into a shape that has adapted the contour of the mould. It is most frequently used to process both polycarbonate and thermosetting polymers, with the quantity use the previous being substantially higher.: 13 Thermoplastics prevail due to features that make them highly ideal for shot moulding, such as ease of recycling, versatility for a variety of applications,: 89 and ability to soften as well as stream on heating.In multiple tooth cavity moulds, each cavity can be similar and develop the same components or can be unique and also develop numerous different geometries during a solitary cycle.
The screw delivers the raw material forward, blends and also homogenises the thermal and viscous distributions of the polymer, as well as reduces the required heating time by mechanically shearing the product and also including a considerable quantity of frictional home heating to the polymer. The product feeds onward through a check valve and gathers at the front of the screw into a quantity recognized as a shot. When sufficient product has actually collected, the material is forced at high pressure and rate right into the component forming dental caries. The exact quantity of shrinkage is a function of the resin being used, and can be fairly foreseeable. To protect against spikes in stress, the procedure generally makes use of a transfer placement representing a 9598% complete tooth cavity where the screw shifts from a constant velocity to a constant pressure control.
8 Easy Facts About Manufacturing Explained
The packaging pressure directory is applied until the entrance (tooth cavity entry) strengthens. Due to its tiny dimension, the gateway is typically the very first location to strengthen via its whole thickness.: 16 Once the gateway solidifies, no even more product can enter the cavity; appropriately, the screw reciprocates and obtains material for the following cycle while the material within the mould cools so that it can be expelled as well as be dimensionally secure.Report this wiki page